Contact us
Strada Biharia nr. 67-77, Sector 1,
Bucuresti 013981, Romania
Tel:
0040 21 599 77 66
Fax: 0040 21 599 77 67
Email: office.ima@ima-metav.ro
marketing.ima@ima-metav.ro
financiar.ima@ima-metav.ro
Foundry
The foundry has modern production facilities for the manufacturing of castings in ferrous alloys (grey cast iron, nodular cast iron, siliceous cast iron, highly alloyed cast iron with chromium, low, medium and high alloyed carbon steels), but also castings in light non-ferrous alloys (aluminium alloys), with different complexity degrees and quality requirements.
There are used following methods of molding-core making:
- Molding with raw mixture method that has bentonite as binder.
Mixture preparation is done on the automatic installation with DISA mixer and the molding is done on the automatic molding machine HSP2, from Heinrich Wagner Sinto which uses SEIATHSU procedure with air injection and pressing with high pressure. The DISA mixer makes at every 2 minutes a batch of 500 Kg mixture, to which it automatically controls the quality and HSP2 machine produces per hour minimum 25 molds with dimensions of 700x550x250/250 mm. The whole technological flow of mixture preparation/molding/pouring/knock out/mixture recycling is computer monitored. - The method of molding with mixture based on sodium silicate, prepared on Minimix, with capacity of 2t/h - for molding unique parts and small series parts - manual molding.
- The process for obtaining cores on the IMAFONT 15 L machine - uses mixture with carbophene binder, hardened with CO2.
The ferrous alloys are developed in air induction furnaces with capacities of 1000 kg and 250 kg, and gravitational poured in molds and cores, after a rigorous control of the chemical composition. Parts with weights of minimum 0.3 kg and maximum 700kg can be obtained.
The aluminium alloys are developed in a dual furnace (melting with marsh gas and maintaining with electricity) with graphite crucible, having a capacity of 500 kg and in two electric furnaces with graphite crucible, with capacity of 200 kg. The pouring is made gravitational in metallic molds on machines of open/close molds and/or in molds and cores from molding sand. We can obtain parts of maximum 250 kg with walls thicknesses of at least 4 mm, roughness of minimum 25 µm ensuring the reproducibility of physical, mechanical and structural characteristics.
The delivered parts include:
- Anodes for cathodic protection for containers and pipelines, oil and gases products
- Bucket excavator teeth in alloyed steel, for mining industry
- Grey cast iron and nodular cast iron parts for pumps and also stainless steel parts
- Components for sandblasting installations in high alloyed cast iron with chromium, nickel and molybdenum
- Urban furniture
- Al alloys castings
Equipment
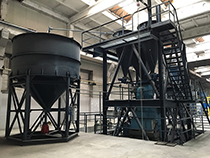
New sand hopper and pneumatic transport pump
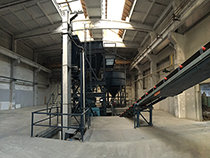
Installation with DISA mixer
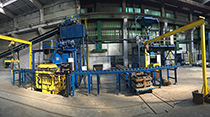
H.W. Sinto HSP 2 Molding Machine
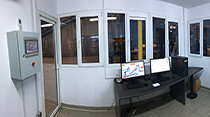
Automation process tracking
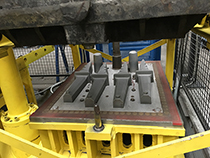
Excavator teeth model plate
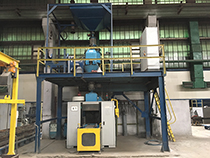
IMAFONT 15 L Core-Making Machine
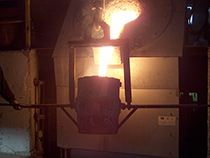
Induction furnace for cast irons and steels
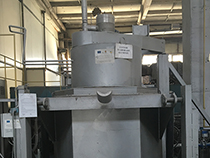
Furnace for aluminium alloys development
Products

Anodes for cathodic protection

Anodes for cathodic protection

Teeth for excavator bucket

Teeth for excavator bucket

Teeth for excavator bucket

Components for sandblasting installations in high alloyed cast iron with chromium, nickel and molybdenum

Urban furniture

Urban furniture

Grey iron and nodular iron pumps components, but also stainless steel castings

Grey iron and nodular iron pumps components, but also stainless steel castings

Grey iron and nodular iron pumps components, but also stainless steel castings

Grey iron and nodular iron pumps components, but also stainless steel castings

Grey iron and nodular iron pumps components, but also stainless steel castings

Al Alloys Castings

Al Alloys Castings

Al Alloys Castings

Cores Mold