Research on designing and processing of high entropy alloys for tough loads
Deadline: 15.11.2013
Phase value: 500,000 lei, of which 200,000 lei grant
Activity I. Research on composition designing of the new types of high entropy alloys
Activity I.2. Research on plastic deformation behavior and heat treatments of high entropy alloys
By definition, each high entropy alloy contains at least five main metallic elements, with atomic concentrations between 5 and 35 %. High entropy alloys (HEA) are composed from n major alloying elements, with n ≥ 5, introduced in equimolar or nearly equimolar reports, which easily lead to formation of simple solid solution phases with c.f.c. or c.v.c. network type, nano - structures or even amorphous states in cast state. Therefore HEA are solid solutions with high strength, good thermal stability and higher hardening capacity than conventional alloys, combined with superior strength characteristics in different environmental conditions. Regarding the properties of alloys from AlCrFeMnNi class, these show a strong resistance to wear up to temperatures of 800 °C, associated with a hardness of up to 800-900 HV after heat treatment.
Taking into account the outstanding mechanical properties of the alloys from AlCrFeMnNi class, for a first batch of test was chosen AlxCrFeMnNi composition, which was modified by varying the Al content in the chemical composition. The materials used to produce these alloys are high purity and were appropriately selected in terms of chemical composition and particle size analysis.
Specimens were collected from representative samples for mechanical and micro-structural characterization (laboratory tests regarding: the microhardness in cast state; heat treatments applied on high entropy alloys from ALXCrFeMnNi class; metallographic study). From the alloy behavior during sampling for metallographic analysis resulted that by increasing the percentage of aluminum it is obtained an increase of metal matrix brittleness. Effect of brittleness is expressed by the tendency of fragmentation to very small forces or on application of loads trough shock, accompanied by the occurrence of some breaking surfaces with a cleavage aspect.
Also, there were studied the plastic deformation mechanisms (processing and variables of material important for forging) and the importance of heat treatments applied on high entropy alloys.
As a result of the foreseen activities in this phase all the proposed objectives were fulfilled in order to obtain the new product.
Results:
- Technical study
- Test lot of high entropy alloys at laboratory scale
- Testing reports
- Acquisition of tangible assets
- Acquisition of intangible assets
- Web page for HEATEETH Project
Research on obtaining and processing the high entropy alloys for tough loads
Deadline: 15.05.2014
Phase value: 1,012,500 lei, of which 405,000 lei grant
Activity II.1 Research on obtaining at laboratory scale high entropy alloys. Testing the micro-structural and mechanical characteristics.
Activity II.2. Research on obtaining at industrial scale the high entropy alloys. Experiments for plastic deformation and heat treatment
The activities of the phase II were based on results obtained in previously phase of the project.
Optimal solution chosen to obtain high entropy alloy from AlxCrFeMnNi class, used for hard facing the teeth of excavator bucket, is to develop HT3 alloy with the following composition: Al-5,73% ;Cr-22.08%; Fe- 23.78%;Mn-23.35% and Ni-25.06%
In the experimental program were taken into account two technological options to prepare HT3 alloy, having the purpose to control better the assimilation of chemical elements, and thus to achieve a composition with a very small variation for each chemical element: Version 1 - elaboration in vacuum induction furnace, closed; inside the furnace it was achieved a level of 100 mbar vacuum; and Version 2 - Elaboration into a furnace with argon protection atmosphere.
The casting of the obtained alloy was made in moulds manufactured from a moulding mixture based on sodium silicate, closed moulds and open moulds;
There were obtained HT3 alloy semi-finished castings, shaped like plates and sticks, which were subsequently subjected to blast cleaning, deformation and heat treatment operations;
The semi-finished parts were machined until there were obtained a welding electrodes with a diameter of 5 mm;
HT3 alloy electrodes were used in preliminary experiments to load the teeth of the excavator bucket, trough WIG welding process;
During the experiments were performed chemical, mechanical and micro-structural characterizations both on samples made from prepared alloy and also on samples hard faced with high entropy alloy.
After making experiments it was concluded that:
- Favorable option for developing high entropy alloy is to prepare it in the vacuum induction furnace, closed furnace, vacuumed and with argon atmosphere;
- For the mould option, using moulding mixture, the most efficient is closed mould. For the next phases of the project there were taken into account other options for obtaining electrodes such as casting in cochila and plastic deformation (extrusion) of the bars cast in moulding mixture.
Photos during the experiments:
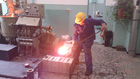 |
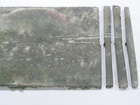 |
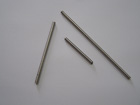 |
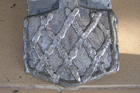 |
Preparation / Casting HT3 |
Semi-finished part from HT3 |
HT3 Electrode |
Element hard faced with HT3 |
Activity II.3. Protection of intellectual property rights
Patent Application – A00354/08.05.2014 " Metallic material with high tenacity and hardness for weld hardfacing and obtaining process, Inventors: Geantă Victor, Voiculescu Ionelia, Ştefănoiu Radu, Binchiciu Horia, Vasile Mihai Ion, Bârlădeanu Mihail, Ionescu Maria, Cârciumăreasa Daniel, Irimia Mihailena
Activity II.4. Results Dissemination
Results:
- Experiments report
- Testing lot for high entropy alloy HT3
- Test reports
- Electrodes from HT3 Alloy
- Testing lot - hard faced teeth with HT3 for excavator bucket
- Patent application
- Articles / poster
Research on loading trough welding of the component excavator using high entropy alloys
Deadline: 15.11.2014
Phase value: 1,387,500 lei, of which 555,000 lei grant
ActivityIII.1 Obtaining excavator component trough casting. Obtaining rods for tough loads from high entropy alloys
Activity III.2. Weldability testing of high entropy alloys and characterization of the material deposited trough welding. Preparing the annual report.
The excavator components were made using, in parallel, two technological processes - preparation of molding mixture for making molds and cores, according to technological instruction code IT-023,- smelting and casting of the manganese steel alloy T35Mn14, according to technological instruction code IT- 024.
There were made 8 lots of teeth for the excavator’s bucket, each group being composed of 3 types of teeth: bucket tooth 1400 modernized, bucket tooth 1400 non-modernized, bucket tooth 1300; they were submitted to blast cleaning and heat treatment and were prepared to be hardfaced with high entropy alloy HEA.
The rods (electrodes) manufactured from HEA alloy and used for hardfacing the excavator ‘s bucket teeth were realized in two stages: - smelting and casting high entropy alloy HEA, from AlxCrFeMnNi class, code HT3 shaped like semi-finished part (bars) and -machining the HEA bars, in form of welding electrodes.
The batches of HEA alloys were prepared in vacuum induction melting furnace and the material was cast either in the molds of loam, either in chill (metal mould) manufactured in the machining department of IMA METAV. HEA semi-finished castings were machined by turning or extrusion operations being obtained welding electrodes with a diameter of 6- 8 mm.
The lots of teeth were hardfaced with HEA electrodes according to "Procedure for TIG welding with high entropy alloys as filler materials" developed in project by UPB –ERAMET partner. To establish the hardfacing technology of teeth for excavator’s bucket we started with the analysis of the stress during operation; top part of the tooth is subjected to violent shock compression and front surfaces are subjected to friction by abrasion. The excavator’s bucket teeth which were hardfaced with high entropy alloy were given into exploitation in pits of CEO.
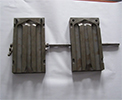 |
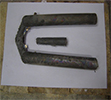 |
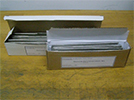 |
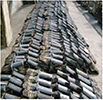 |
Chill for casting |
HEA semi-finished part |
HEA welding electrodes |
Teeth for excavator's bucket hardfaced with HEA electrodes |
Results dissemination
Results:
- Experiments report
- High entropy alloy HT3 batches
- Lot of HEA welding electrodes
- Lot of excavator bucket teeth hard-faced with HEA electrodes
- Test reports
- Procedure for TIG welding with high entropy alloys as filler materials
- Technical documentation for welding
- Achievement market indicator
Testing the excavator components in execution and working conditions
Deadline 30.11.2014
Phase value: 1.260.000 lei, of which 600.000 lei is non-refundable
Activity IV.1 Development of welding technology . Optimization of the welding parameter scheme. NDT testing.
Activity IV.2. Testing excavator components in working / Internal homologation / Development of manufacturing technology
Activity IV.3. Dissemination / Results promotion
During this phase, the involved partners have participated according to the project implementation plan and conducted the following activities:
- Finalization of welding technology and optimization of welding parameters;
- Preparing non-destructive testing procedure for excavator bucket's teeth which were hard-faced through WIG welding using high entropy alloy (HEA ) materials - Working procedure for penetrating liquids inspection -PLLP No.1 / 066.1 / 2012.
- Execution of experimental lots;
- Execution of homologation lot of HEA alloy electrodes;
- Manufacturing of HEA alloy hard faced teeth Lots for testing and homologation;
- Chemical, mechanical and micro-structural characterization of the products;
- Testing in operation of the manufactured lots;
- Homologation of the innovative product;
- Finalization of technical documentation for the product achieved;
- Dissemination and promotion of results;
The implementation of activities from Phase IV has contributed to fulfilling all envisaged goals.
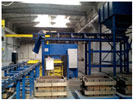 |
 |
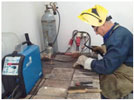 |
Automatic moulding machine HSP2 |
HEA -High entropy alloy electrodes |
Hard-facing using HEA |
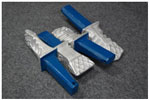 |
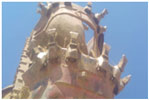 |
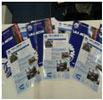 |
Teeth for excavator's bucker hard faced with HEA. |
Testing in operation |
|
Results dissemination
Results:
- Technological instruction - Preparing and casting the HEA for hard-facing - Code: IT-029
- Technological flow for plastic deformation processing of the HEA electrodes
- Technological sheet for plastic deformation processing No.4357 M
- Technological sheet for innovative product
- Experimental lots for innovative product
- WIG - WPS welding procedure no. DPST0066/2015
- Procedure for non-destructive testing of the HEA hard-facing teeth, PLLP1/066.1
- Homologation lot
- Testings reports
- Homologation protocol
- Accomplishment report